Product
Raw Material
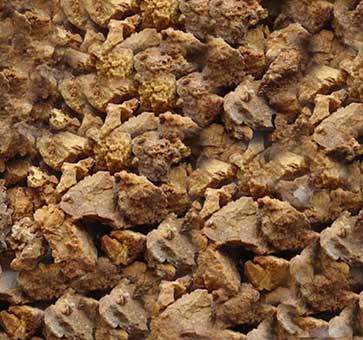
JBTC offers raw materials for production of shaped and unshaped refractories and a number of other chemical products since the cost of new high grade material i.e. Magnesia, Alumina, Chrome and Dolomite is so high we supply only A Grade Raw material in form of USED REFRACTORY MATERIAL in properly inspected Condition Mined from Austria, Russia, Ukraine and far-off foreign countries. This is done to make the production cost feasible and an Eco-Friendly way.
New Virgin raw-materials can also be procured as per the demand.
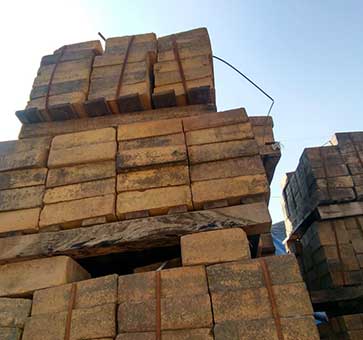
Our main raw material are from Austria, Italy and Turkey, more than 1 million annual tonnes of high grade refractory raw materials magnesite and dolomite are extracted in underground and surface mining and processes on site we purchase the raw materials as per the customer’s requirement alternatively provide them low cost options also.
We have established comprehensive refractories knowledge – from raw materials to applications in all relevant industries – and especially understanding of refractories in all application processes.
New ideas for product and system development are constantly accumulated, evaluated and integrated into the Research & Development program.
In the common language materials are called refractory if they are applied at temperatures above 600 °C. But in our company we define materials into three basis :
- Heat resistant below 1500 °C
- Refractory min. 1500 °C
- Highly refractory min. 1800 °C
Comprehensive quality management is of special importance to the quality of our products.
JBTC is strongly orientated to develop new raw materials and products to increase service lifetime and customer satisfaction.
Magnesia Bricks
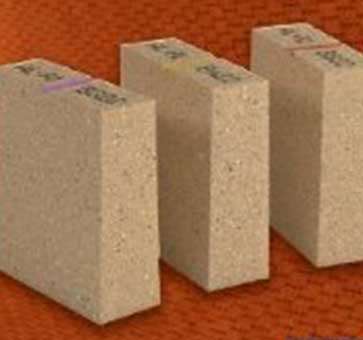
JBTC offers exclusive range of Magnesia Bricks of top notch companies as well as its own lineage.
Magnesia Bricks are basic refractory materials different grade magnesites used as raw materials produce Magnesia bricks of various qualities. MgO materials are used extensively in basic oxygen and electric arc steelmaking refractories.
Magnesia Bricks can be divided into two categories of Burnt Magnesia Bricks and Chemical Bonded/Fused Magnesite Brick. They have excellent performance of superior high temperature mechanical strength and volume stability.
Burned Magnesite brick :
- Material and Technique : burned magnesia as raw material
- Property : good high-temperature performance, strong slag resistance
- Application : used in permanent linings of EAF and steel Convertors, lime kilns, glass tank regenerators, torpedo cars and non-ferrous furnaces
Fused Magnesite brick :
- Material and Technique : made from fused magnesia, shaped under high pressure, fired under ultra high temperature and finished with post technical treatment
- Property : high bulk density, good high-temperature performance and strong hydration resistance
- Application : used in the tapping hole of the convertor with severe slag corrosion and wear, the slag line of non-ferrous furnaces, the tapping hole of metal mixer furnaces, and chimney block of glass tank regenerator
The protection of MgO and MgCr bricks against hydration by means of impregnation with an aqueous kieserite solution is done through state-of-the-art technology and offers sufficient hydration protection under normal circumstances
Mag Chrome Bricks
JBTC offers exclusive range of MAG-CHROME bricks as per the customer demand we have the bricks from world leaders in refractory as well as our own lineage.
Magnesite Chrome Brick is made of some preliminary synthesis high purity raw materials. The high purity raw refractories should be high pressure formed, ultra high temperature fired and then go through some other post-treatment process and system, finally made the magnesite chrome brick. The magnesia chrome brick has high room temperature compressive strength, low porosity, strong erosion resistance and scouring resistance, etc.
There are three types of Mag-Chrome bricks :
Ordinary Magnesite Chrome brick :
- Material and Technique : made from sintered magnesia and chrome ore and sintered at high temperature
- Property : having higher bulk density and stronger thermal resistance than the magnesite brick
- Application : used in cement rotary kilns, glass kiln regenerators, permanent lining of steel furnace permanent and refining ladle permanent lining of refining ladle.
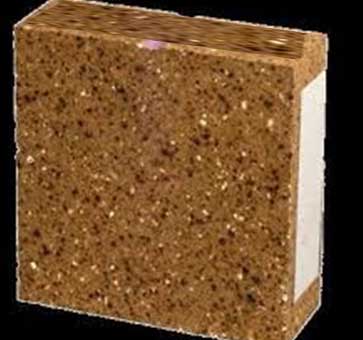
Direct-Bonded Magnesite Chrome brick :
- Material and Technique : made of low impurity chrome ore and high purity magnesia and fired at high temperature over 1700?
- Property : strong slag resistance and good performance under high temperature
- Applied in cement rotary kilns, electric arc furnaces, and non-ferrous metal furnaces
Rebonded Magnesite-Chrome brick and Semi-Rebonded Magnesite-chrome brick :
- Material and Technique : made with synthetic fused magnesia, shaped under high pressure and fired at ultra high temperature
- Property : Thanks to the high purity of the raw material, the product has good high temperature performance, high thermal resistance, low air-permeability, and strong slag resistance
- Application : used in tapping hole of AOD furnace, the lower vessel of vacuum chamber and snorkel of RH furnace, and the slag line of high temperature furnaces.
High Alumina Bricks
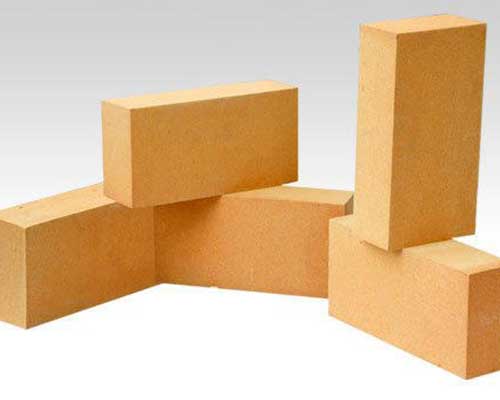
JBTC offers exclusive range of HIGH ALUMINA bricks with various qualities we guarantee our bricks to be of superior quality.
The term High Alumina refers to the bricks having AL203 content of 47.50% atleast or higher
High alumina bricks require bauxite to be manufactured. Bauxite is a naturally occurring mineral which is also found in kaolin-tic clays. These two substances are taken as raw materials and roasted together to produce a high refractory material.
This material is used to make high alumina bricks that find applications in not only kilns and furnaces but also cement, iron and steel, and glass industries. Our high alumina bricks are not only very hard and thermal resistant but also good at electrical insulation.
High-alumina brick are resistant to acid slags, that is, those high in silica. Basic components in slag, such as MgO, CaO, FeO, Fe2O3 and MnO2 react with high-alumina brick, particularly brick high in silica. As Al2O3 content increases, slag resistance generally improves
We offer these bricks with varying percentages of alumina and Fe2O3 and in different shapes and sizes according to the requirement.
High alumina brick is a kind of neutral refractories. It is manufactured from bauxite or other refractory raw materials within high alumina formed by molding and calcination. High aluminum refractory bricks has high refractoriness, high load softening temperature, thermal shock stability, good slag resistance, acid, alkali, peeling resistance, erosion resistance and so on.
High alumina brick is mainly used for electric furnace top, blast furnace, hot air stove, ladle, cement kiln, glass kiln and other thermal furnace lining. High alumina brick is widely used in iron, steel, chemicals, cement and other industries.
We have different kind of High Alimuna Bricks mainly :
60% Alumina Grade :
The 60% alumina class is a large, popular class of products. These brick are used in the steel industry, as well as rotary kilns. Brick in this class are made from a variety of raw materials. Some are produced from calcined bauxitic kaolin and high purity clay to provide low levels of impurities. As a result of firing to high temperature, these brick have low porosity, excellent hot strength and creep resistance, and good volume stability at high temperatures.
70% Alumina Grade :
This is the most frequently used high- alumina product class because of its excellent and cost-effective performance in multiple environments. Applications include the steel-industry and cement and lime rotary kilns. Most brick in this class are based on calcined bauxite and fireclay. Brick are usually fired to fairly low temperatures to prevent excessive expansion in burning which causes problems in final brick sizing. Expansion is caused by reaction of the siliceous ingredients with bauxite to form mullite. The brick typically undergo large amounts of secondary expansion when heated. This is advantageous in reducing the size of joints between brick and providing a tight vessel structure, e.g., a rotary kiln. A higher cost and higher quality alternative to producing a 70% alumina brick is represented by brands based on high purity calcined bauxitic kaolin. These brick have superior high temperature strength and refractoriness and significantly lower porosity than typical products based on calcined bauxite. Due to their more homogeneous structure, they show somewhat less expansion on reheating than bauxite-based products.
80% Alumina Grade :
These products are based primarily on calcined bauxite with additions of various amounts of other fine aluminas and clay materials. They are usually fired at relatively low temperatures to maintain consistent brick sizing. Most brick in this class have about 20% porosity, good strength and thermal shock resistance. Because they are relatively inexpensive, perform well and are resistant to most slag conditions present in steel ladles, they are used extensively in steel ladle applications.
90% and 99% Alumina Grade :
These brick contain tabular alumina as the base grain and may include various fine materials such as calcined alumina, clay and fine silica. As these brick generally have low impurity levels, alumina and silica typically make up 99% of the chemical composition. Usually, the only mineral phases present are corundum and mullite. Properties such as high hot strength, creep and slag resistance benefit from this purity level.
Low Alumina Bricks
JBTC offers exclusive range of LOW ALUMINA bricks with various qualities we guarantee our bricks to be of superior quality.
The term Low Alumina refers to the bricks having AL203 content lower than 47.50%.
They are designed primarily for ladles. These 50% lower alumina class brick have low porosity and expand upon reheating to 2910°F (1600°C) - desirable features for ladle applications since they minimize joints between brick, giving a near monolithic lining at service temperature.
These brick are also characterized by low thermal expansion and good resistance to spalling. Many high-temperature industries use them as backup brick,alumina products based on high purity bauxitic kaolin, and other ingredients in the matrix, provide exceptional load-bearing ability, alkali resistance and low porosity. These qualities make such brick an excellent choice for preheater towers and calcining zones of rotary kilns.
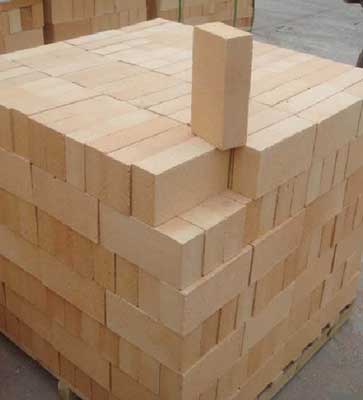
Nozzle
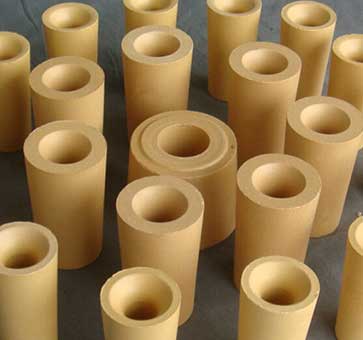
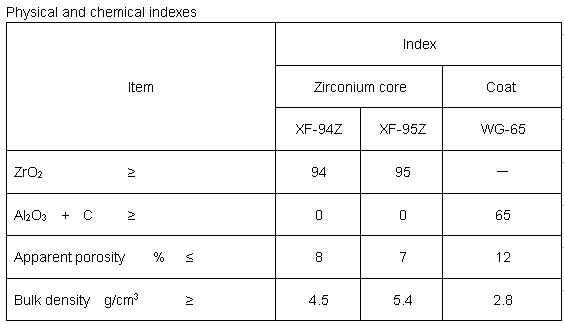
JBTC offers exclusive range of NOOZLES with various qualities we guarantee our material to be of superior quality.
Nozzles are continuous casting refractories that play an important role in controlling the flow of molten steel during steel making process.
JBTC manufactures alumina carbon fired and magnesia carbon fired nozzles that are used by our clients in various industries. We can make these as per specifications and industrial use of our clients. One big problem faced by clients involved with steel manufacturing is the clogging of the walls of nozzles. Also, these nozzles also get eroded quickly because of inclusion of metallic impurities. These impurities sinter and get attached to the walls of nozzles that are made from alumina refractories. These problems have been seen to lead to inclusion problems in the cast product. But the nozzles made by JBTC are free from clogging even after continuous use in steel making process. This is the reason these nozzles are in high demand among the clients.
Nozzle has the advantages of heat preservation, reduce the temperature of the outer surface of the nozzle, reduce the heat dissipation, reduce weight, increase strength, improve the service life, etc.

Stopper
JBTC offers exclusive range of STOPPER with various qualities we guarantee our material to be of superior quality.
Our Isostatically pressed nozzles for foundry applications have the following qualities :
- High dimensional stability
- Long service life
- Consitant casting times
- Low slagging
- Individually designed
- For all receptor systems
All our Monoblock Stoppers are finished according to client specifications and are available with specially formulated nose Armour Glaze hardening characteristics giving enhanced erosion and abrasion resistance.
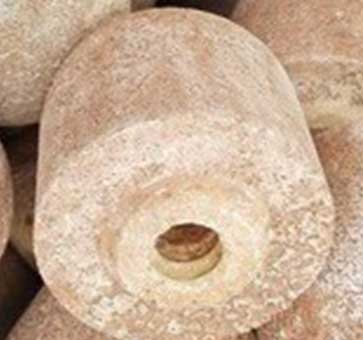
Fire Clay
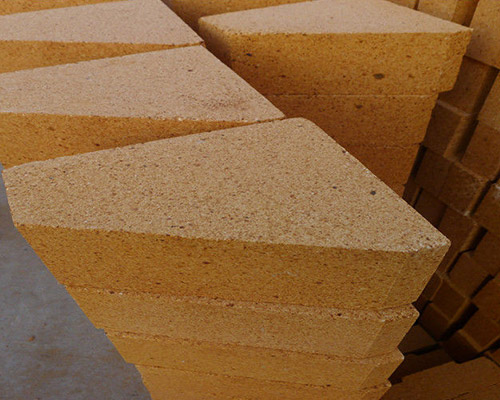
JBTC offers exclusive range of FIRE CLAY BRICKS with various qualities we guarantee our bricks to be of superior quality.
Fire-clay refractory bricks are essentially hydrated aluminum silicates with minor proportions of other minerals. As a type these refractory bricks are extremely versatile and therefore can be put to numerous uses. These bricks are usually least costly of all refractory bricks and are extensively used in various industries including iron and steel industry, nonferrous metallurgy, glass industry, and cement industry. Fire Clay bricks, using high alumina bauxite as raw refractory material which is being carefullly selected and then be shaped and burn in tunnel kiln, finnaly made the clay brick.
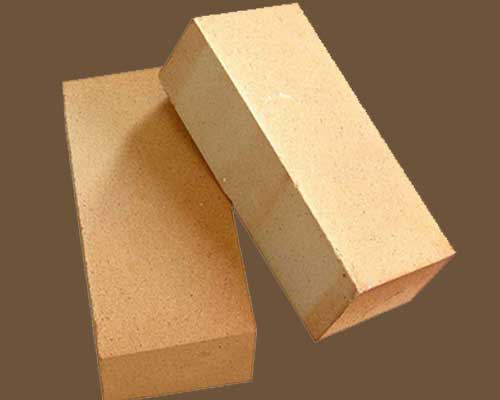
Fire-clay refractory bricks are essentially hydrated aluminum silicates with minor proportions of other minerals. As a type these refractory bricks are extremely versatile and therefore can be put to numerous uses. These bricks are usually least costly of all refractory bricks and are extensively used in various industries including iron and steel industry, nonferrous metallurgy, glass industry, and cement industry.
Fire Clay bricks, using high alumina bauxite as raw refractory material which is being carefullly selected and then be shaped and burn in tunnel kiln, finnaly made the clay brick. Clay bricks is very cheap, it is the best choice for normal high temperature kiln. Clay bricks is one kind of weak acid refractory products, it can resist erosion from acid slag and acid gas.
Clay brick's thermal performance is good, it also has good resistance to rapid cooling and hot. Clay refractory bricks are widely used in blast furnace hot stove, carbon roaster and other high temperature furnace which have an higher requires in Load softening temperature.
Laddle Sleeves
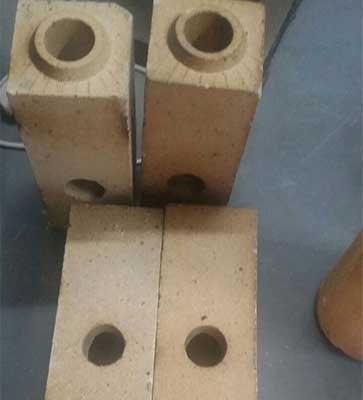
JBTC offers exclusive range of LADDLE SLEEVES with various qualities we guarantee our material to be of superior quality.
Ladle Sleeves are manufactured using high grade raw material and advanced technology by our professionals. The offered range are widely demanded for applications like lining furnaces, kilns, fireboxes, boilers, etc. Known for fine finish, high strength, durability and ability to withstand extreme temperature & pressure, these are available in various sizes and shapes to fulfill the wide demands of the clients.
Aluminum transfer ladles require an abrasion resistant not wetting castable. These castables also need to be able to take repeated thermal shock stresses. The completed ladles also have to be able to take physical abuse. We have a selection of non-wetting castables for this demanding application.
The pouring spout often experiences greater amounts of wear when compared to the rest of the ladle. We can also offer custom replaceable inserts for just the pouring spouts of your existing designs.
We also have experience relining ladle lids for your transfer applications. No transfer ladle is complete without a lid. The increased heat retention leads to increased transfer times. The lids also keep your personnel safe from splashes.
We offer these Fire Resistant Ladle Sleeves to our valuable clients at industry leading prices.
Refractory Bed Material
JBTC has its own superior class plants and engineering team for bed material production as well as sorting facilities. Refractory bed material is heat resistant material that is mainly used inside furnaces, kilns, reactors and incinerators. These materials have strong physical and chemical properties that make it bear extremely high temperatures and remain stable. Refractory bed material is often made from a variety of natural and synthetic ingredients and combinations of compounds and minerals such as fireclays, alumina, chromite, bauxite, silicon carbide, magnesite, dolomite, zirconia and others
The material should be able to expand and contract uniformly with temperature change without cracking.
Bed materials of refractory material should have sufficient mechanical strength and be able to withstand various forces like
- Vibration action
- Cutting & abrasive action of frame
- Flue dust
- High temperature
- Sudden changes of temperature
- Load at service conditions
- Chemical and abrasive action of operational phases
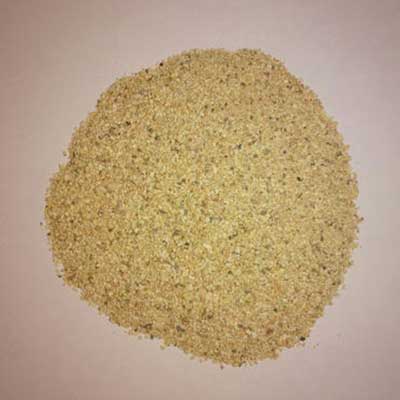
We use the latest technology and quality raw materials to offer durable products. We value our clients and ensure their satisfaction. Our feedbacks and interactions with our clients help us evolve and improve continuously. We offer the right products at the right price, which makes us one of the most reliable refractory bed material exporters.
The Boiler Bed Material is the most critical product for Boiler operation. It is not just the crushed refractory grog. It is the lifeline for Fluidized Bed Boilers.
The product is processed from special Refractory aggregates of high chemical purity, dense consistency, and high refractoriness. It is apposite to sustain technical properties for fluidization at high temperatures up to 1400°C under most critical working conditions. The product is designed with special attention to its very uniqueness and service necessities.
Mag Carbon Bricks
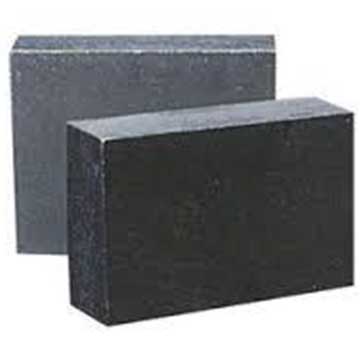
JBTC offers exclusive range of MAG-CARBON as per the customer demand.
Magnesia-carbon bricks are resin bonded bricks containing high-purity fused and or sintered magnesia and flake graphite as their main ingredients.
Magnesia carbon bricks have excellent corrosion resistance together with good thermal shock properties.
Magnesia carbon brick takes use of fused magnesia sand, high carbon graphite as raw material, adding proper amount of antioxidants, bonded with phenolic resin,made by high pressure molding. Good erosion resistance and shock resistance. Generally used in furnace lining.
Megnesite-Carbon brick is the non-fired basic refractory material. It improves the corrosion resistance and slag resistance to add a certain amount of graphite. Due to their different functional zones, Carbon containing Products made of various chemical components are produced by choosing the appropriate raw material and composite addictive.
Magnesia carbon brick
- Material and Technique : Magnesia-Carbon brick is resin-bonded brick made from dead-burned or fused magnesia and graphite. Anti-oxidant is added if required.
- Properties : Magnesia-Carbon brick has good performance in thermal resistance, corrosion resistance and spalling resistance.
- Application; widely used in converters, EAFs, ladles and refining furnaces
BLOCKS
JBTC offers exclusive range of BLOCKS with various qualities we guarantee our material to be of superior quality.
Big Block are used primarily for furnace walls. We have also worked on large monolithic precast shapes such as furnace ramps, holding furnaces, and deltas. JBTC can accommodate your big block needs. From one ton to several tons, we have the capacity and experience to complete your projects. We have a full line of in-house castables to choose from, or we can work with any major manufacturers’ castables.
Precast Burner blocks, or burner tile, are essential items for industrial processes. Large projects with limited lead time are our specialties. If you have your own tile shop, we can provide quality castable materials to cast your blocks from. We can also toll fire your shapes or provide casting/firing consultation services. We have a manufacturing team experienced at completing everything from complicated ring burner tile systems to single piece burner tiles.
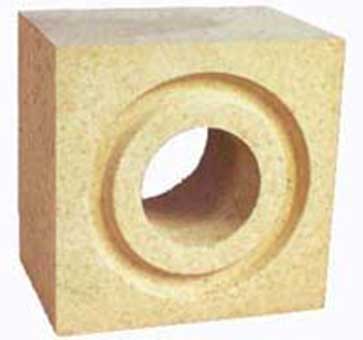